Case Study
Norfolk International Airport runway case study: pulling an all-nighter — 48 days in a row
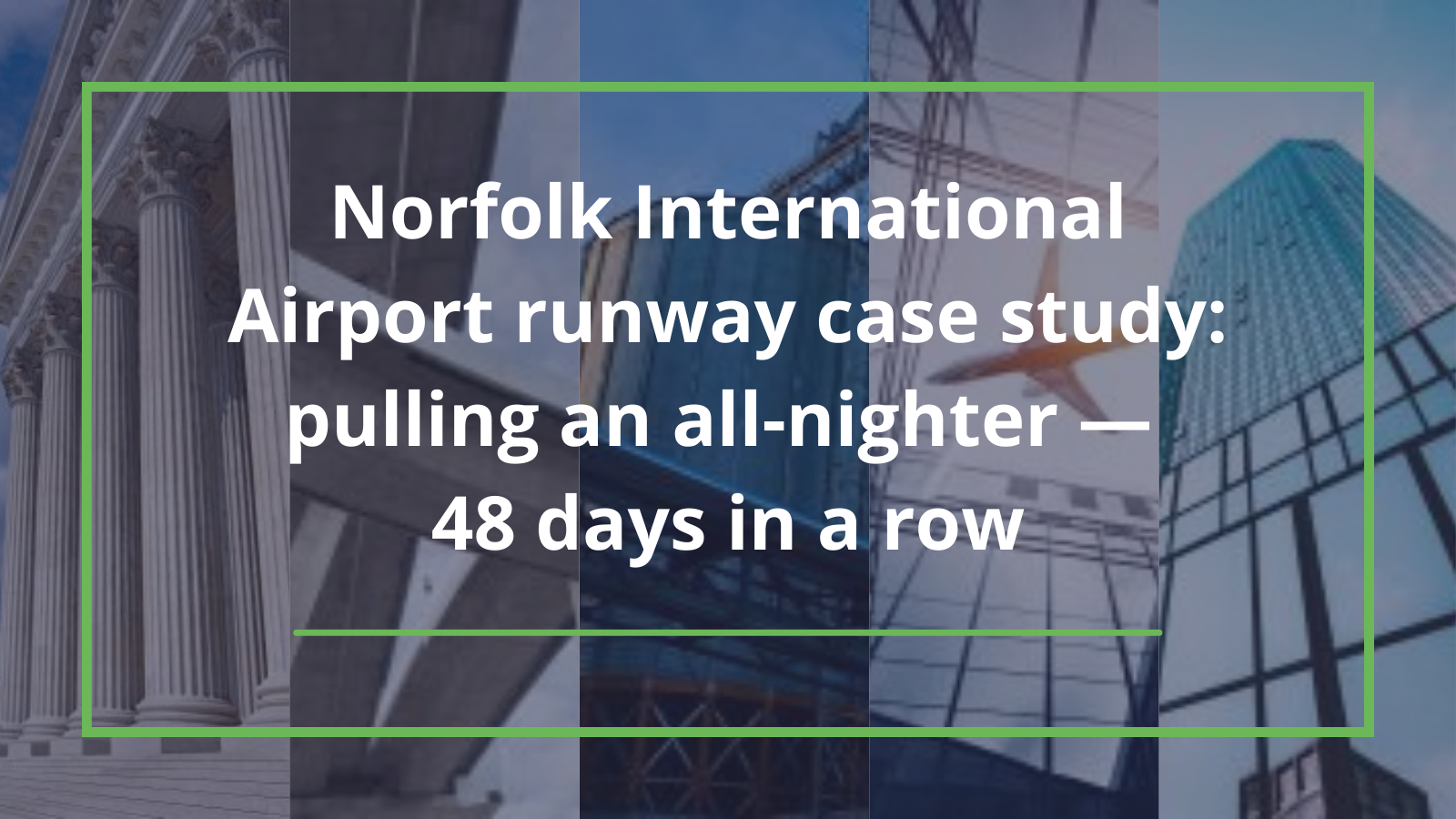
Norfolk International Airport (ORF) is one of the busiest airports in Virginia. Over 3.3 million passengers fly in and out each year, and about 70 million pounds of air cargo are shipped to and from Norfolk. Airport officials, major airlines, fixed-base operators, customs brokers, the FAA, military personnel and thousands of employees must navigate the 1,300-acre facility in careful coordination to ensure seamless operation and safety.
What happens when its sole commercial runway requires major rehabilitation? ORF can’t ground flights, and a 24/7 international airport can’t “close for maintenance.”
The success of the Norfolk Airport Authority’s extensive, multi-phase construction project hinged on meticulous planning, strict scheduling and crews choreographed to perfection. Connico’s extensive cost estimating and project management expertise were integral components of the project’s success.
Runway 5-23 under distress
In 2015, ORF personnel discovered that the centerline lights on Runway 5-23, its only commercial runway, were out of grade tolerance. To meet strict FAA requirements, maintenance crews applied a temporary, tedious fix - but a permanent solution still needed to be implemented.
Their investigation uncovered that all of the centerline light cans in the 6,000-foot section in the center of the runway, ORF’s original runway before it was extended on either end, were affected. Additionally, a runway evaluation uncovered issues with this original 1940’s asphalt and the two 40-year-old, 1,500-foot concrete end extensions. The airport needed a permanent solution, and quickly.
Prime design engineer Kimley-Horn engaged Connico to develop the project estimate and undertake an on-the-ground management role.
Connico’s role on this big, busy, beautiful team
Planning began more than 10 months before any work actually started on the project. We worked alongside team members from Virginia Paving Co., the project’s prime contractor, and their team of qualified subcontractors and suppliers from across the country. We approached the project as a partner with not just Kimley-Horn and the airport staff, but with the contractor as well. Our role included:
- Coordinating and scheduling:
- Coordinating with airport staff to help publish the correct runway closures, and ensure the closures were communicated to ATC and airlines ahead of time
- Collaborating with fixed-base operators to clear the runway at night, ensuring the availability of taxiways for FBO night operations on the airfield
- Discussing concrete mix design: the short 5-hour work window required concrete with an extremely high, early set strength and time (measured in minutes), so the mix design was a critical piece of the project
- Consistently communicating with the team on timing
- Contingency planning: There were contingency plans for everything. Everything. For example, if an excavator broke down, we had a 220-ton crane on standby. If crews couldn’t drive it, they’d bring in the crane, pick it up and take it offsite.
- Maintaining open communication — day and night
Engineers, the FAA and ORF officials were working their normal schedules, not our schedules. We had to plan carefully and address concerns the day BEFORE a work shift. Since there were multiple stakeholders, it was critical we were all on the same page. Connico helped facilitate communication with the FAA, ORF officials, the airport’s operations department, Kimley-Horn, security personnel and the contractors and their crews.
Key strategies of our collaborative efforts included:
- Quality testing coordination: During daylight hours, we assessed quality materials testing results and scheduling, ensuring project needs and timelines were being met to the letter.
- Watching the weather: Collaboratively with the contractor, we made the go/no go call by 11:30 p.m. each night because getting caught in inclement weather was a significant concern.
- Answering questions: There were of course situations in which the field conditions surprised us and didn’t match up with our plans. Since we were running these short-timeframe night shifts, our ability to apply engineering judgment was crucial in project problem-solving.
“Open-heart surgery on the runway”
The biggest challenge we faced during this project was the clock. We were given the runway at 12:15 a.m. and had to have it ready to return to operation no later than 5:15 a.m. After ensuring equipment was set up per FAA standards, we started work around 1 a.m. and usually began cleanup at 4:30 a.m.
There was no room for error or tolerance for an extra minute here or there. The runway needed to be completely clear and ready by 5:15 a.m. every morning, which left about 3.5 hours to work.
In that short window, more than 150 crew members worked together like a well-oiled machine. The project was described as “open-heart surgery on the runway,” and it’s an apt analogy; we had to “cut open” the runway, complete the scheduled repair work and suture it back up so normal ORF operations could resume. The stakes were high.
Our schedule was the same seven days a week from early August to late October in 2018. Not one, but two hurricanes stalled labor during the job, but only for a total of five days. The contractor worked to keep the project on schedule during weekends or even during minor inclement weather, with their crews busy coring, saw cutting and completing other necessary tasks.
We were never late
Our team was successful in delivering behind-the-scenes service and support that kept the project on track. There was never an us vs. them attitude - we were all in it together.
It’s tough for disparate teams come together like this, under unforgiving project constraints, and display the level of teamwork, collaboration and communication we experienced on the ORF project. But with the aggressive timeline, intense scheduling demands and constant pressure, nothing else would have sufficed. As a result, our team was never late reopening the runway, and the project was completed right on time.
To read more about this project, head over to this featured article in Airport Improvement.